The Importance of Special Refractories
Refractories are materials that can withstand high temperatures and thermal stresses without breaking down. They are essential in industries such as steel production, cement manufacturing, glassmaking, and non-ferrous metal refining, where heat and chemical resistance are paramount.
Special refractories are critical in extending the operational life of industrial equipment and ensuring safe and efficient operations in extreme conditions. These materials play an essential role in maintaining the integrity of high-temperature furnaces, kilns, and reactors, helping to minimize downtime and increase production efficiency.
Further reading: What Are the Special Refractories Widely Used in Modern Industry?
Characteristics of Special Refractories
The unique characteristics of special refractories make them essential for high-temperature applications:
- High Melting Point: Special refractories must withstand extreme temperatures without melting or deforming. This property is essential for industries like steelmaking and glass production, where temperatures regularly exceed 1,500°C.
- Chemical Resistance: The refractories used in high-temperature industries must be resistant to various aggressive chemicals, including acids, slags, and molten metals. This is particularly crucial in industries like steel and aluminum production.
- Thermal Shock Resistance: Special refractories must maintain their integrity when exposed to rapid changes in temperature. This is especially important in cement kilns and glass furnaces, where the thermal cycling can be severe.
- Mechanical Strength: Refractories need to withstand mechanical stresses caused by thermal expansion, pressure, and impact. Materials like magnesia-carbon bricks provide both thermal stability and mechanical strength.
Applications in Key Industries
1. Steel Industry
The steel industry is one of the largest consumers of refractories, accounting for around 70% of global refractory demand. Refractories in steel production are used in various furnaces, including blast furnaces, converters, electric arc furnaces, and ladles. Each part of the steelmaking process requires different refractory materials to handle the varying conditions and temperatures.
.jpg)
- Blast Furnaces: High-quality materials such as clay bricks, high-alumina bricks, and carbon-based refractories like silicon carbide (SiC) are used in blast furnaces. These materials must resist severe thermal stresses and corrosion from molten iron and slag. Advances in SiC-based materials have significantly improved the lifespan of blast furnaces, especially in areas like the furnace body, where temperatures can reach over 1,600°C.
- Electric Arc Furnaces (EAF): In electric arc furnaces, which operate at even higher temperatures, refractories such as magnesia-chrome bricks and MgO-C (magnesium-carbon) bricks are often used. These refractories must withstand the extreme heat generated by electric arcs and resist the corrosive effects of molten steel and slag.
- Ladle Furnaces and Ladles: For ladle furnaces, which are used to refine steel, magnesium-carbon bricks and high-alumina refractories are commonly used to maintain high structural integrity under the intense conditions.
2. Cement Industry
The cement industry relies heavily on refractories in its rotary kilns, where clinker is produced at temperatures exceeding 1,400°C. The demand for refractory materials here is driven by the need for excellent thermal stability, resistance to chemical corrosion, and durability under extreme conditions.
.jpg)
- Kiln Lining Materials: Magnesium-alumina spinel bricks, high-alumina bricks, and non-chromium refractories are widely used in cement kilns. With environmental regulations becoming stricter, chromium-free refractories have gained popularity, reducing the risk of chromium leaching into the environment.
- Preheaters and Coolers: In the preheating zone, refractories like high-alumina bricks are used for their resistance to thermal shock and wear. In the cooling zone, lower-alkaline refractories are used to withstand the thermal cycling and prevent degradation from the rapid cooling rates.
3. Non-Ferrous Metal Industry
Non-ferrous metals such as aluminum, copper, and zinc require specialized refractories due to the high temperatures and the corrosive nature of the metals involved in the smelting and refining processes.
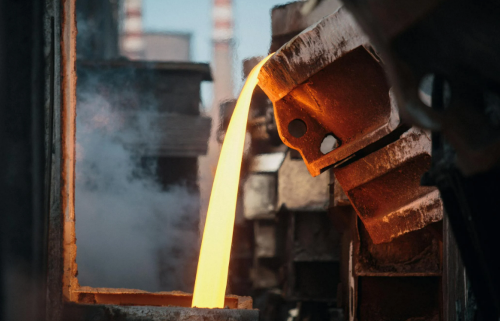
- Aluminum Smelting: Refractories used in aluminum smelting furnaces, such as magnesia-carbon bricks, must withstand temperatures up to 1,000°C and resist chemical attacks from molten aluminum and its impurities.
- Copper and Zinc Smelting: Copper and zinc smelting requires refractories that can handle not only high temperatures but also the acidic or basic slag. For instance, magnesia-alumina and alumina-zirconia refractories are frequently used in smelting operations to resist both thermal shock and corrosion.
4. Glass Industry
Glass production is a highly demanding process that requires refractories with exceptional resistance to heat, chemical attack, and thermal shock. In particular, glass melting furnaces require materials that can endure continuous exposure to molten glass, which can be highly reactive with the refractories.
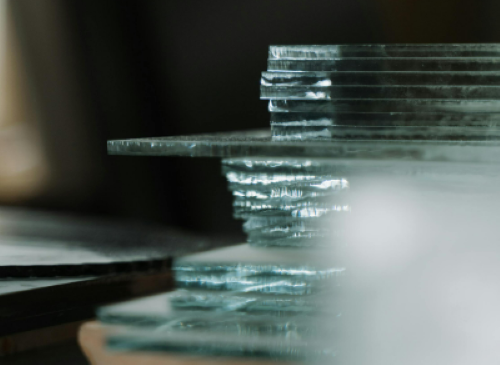
- Furnace Linings: Zirconia-based refractories, such as zirconia-mullite and zirconia-silica bricks, are commonly used in glass furnaces to improve resistance to corrosion and thermal shock.
- Regenerators and Combustion Chambers: Magnesia and magnesia-chrome bricks are used in regenerator chambers for their ability to absorb and release heat efficiently, ensuring the energy efficiency of the furnace.
Conclusion
Special refractories are indispensable for industries that deal with high temperatures and harsh chemical environments. From steel production to glass manufacturing, these materials ensure the safe and efficient operation of furnaces, kilns, and reactors. As industries advance, the need for high-performance, specialized refractories capable of meeting the growing demands of modern high-temperature applications continues to rise. For more information, please check Advanced Refractory Metals (ARM).
REVIEWS
{{viewsNumber}}
Thought On "{{blogTitle}}"
LEVE A REPLY(Cancle reply)
Your email address will not be published. Required fields are marked*
{{item.children[0].name}}
{{item.children[0].created_at}}
{{item.children[0].content}}
More Replies
LEAVE A REPLY
Your email address will not be published. Required fields are marked*