Introduction
Niobium C103 alloy is a widely used high-performance material in industries requiring excellent strength and heat resistance. Composed primarily of niobium (Nb) with additions of hafnium (Hf) and titanium (Ti), this alloy exhibits impressive characteristics, making it an ideal choice for various demanding applications, particularly in aerospace and high-temperature environments.
What Is Niobium C103 Alloy?
Niobium C103 is a refractory metal alloy known for its excellent thermal stability, strength, and ductility. The alloy is typically composed of 89% niobium, 10% hafnium, and 1% titanium. The presence of hafnium and titanium enhances the alloy's mechanical properties, particularly at elevated temperatures. These features make Niobium C103 well-suited for environments where other materials would weaken or fail under extreme thermal conditions.
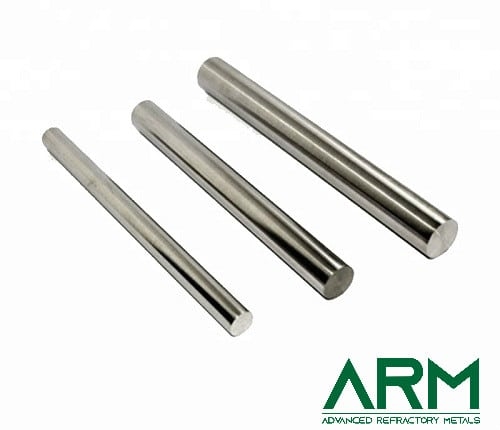
This alloy is particularly useful in the aerospace industry, where components must operate reliably in the high-heat environments of rocket engines and propulsion systems.
Related reading: 10 Important Uses of Niobium
Outstanding Features of C103 Alloy
Niobium C103 boasts several outstanding features that make it unique among high-temperature alloys:
- High Heat Resistance: C103 can withstand temperatures exceeding 1,500°C, retaining its strength and form in extreme heat. This makes it an ideal material for rocket nozzles and engine components.
- Good Ductility and Formability: Despite its high strength, C103 maintains excellent ductility, allowing it to be formed into complex shapes and thin-walled structures. This is essential for designing lightweight, high-performance aerospace parts.
- Corrosion Resistance: Niobium C103 is highly resistant to oxidation and corrosion in various aggressive environments. Its ability to resist degradation in challenging conditions extends the lifespan of components made from this alloy.
- High Strength-to-Weight Ratio: The alloy provides a balance of high strength and low density, which is crucial in applications where weight savings are critical, such as aerospace and space exploration.
Applications of C103 Alloy
Due to its remarkable properties, Niobium C103 is used in a wide range of applications, particularly where extreme temperature and pressure conditions are encountered:
- Rocket Engines and Propulsion Systems: One of the most common uses of Niobium C103 is in rocket engine components such as nozzles and thrusters, where it can maintain structural integrity under high heat and stress.
- Spacecraft Components: The material’s lightweight nature and high heat resistance make it a top choice for spacecraft parts, including shielding and structural components in reentry vehicles.
- Gas Turbines: In the energy sector, C103 is used in the manufacture of gas turbines, which require materials capable of withstanding the high temperatures produced during operation.
- Medical Devices: Niobium's biocompatibility has led to its use in some specialized medical applications, such as implants and surgical devices.
C103 Alloy vs Other Super Alloys
When comparing Niobium C103 to other superalloys, several factors come into play, including heat resistance, corrosion resistance, and mechanical properties. Some common comparisons include:
- C103 vs Inconel: Inconel is a nickel-based superalloy known for its excellent strength at high temperatures, but Niobium C103 surpasses it in heat resistance, particularly at temperatures exceeding 1,500°C. Inconel may offer better oxidation resistance, but C103’s lighter weight makes it a preferred choice for aerospace applications.
- C103 vs Hastelloy: Hastelloy is well-regarded for its corrosion resistance in harsh chemical environments, but Niobium C103 has better performance in high-heat aerospace and turbine applications. Hastelloy tends to be heavier, making C103 advantageous in weight-sensitive projects.
- C103 vs Titanium Alloys: Titanium alloys like Ti-6Al-4V are often used for their strength and lightweight nature, but they lack the extreme heat resistance that C103 provides. While titanium is common in aircraft frames and medical implants, Niobium C103 is preferred in situations where temperatures exceed the capabilities of titanium alloys.
As a leading supplier and manufacturer, Advanced Refractory Metals (ARM) offers a comprehensive range of niobium products, including pure niobium, niobium alloys, and oxides, available in diverse forms such as sheets, plates, rods, wires, tubes, strips, foils, and oxides. Our high-quality niobium products and super alloy products are designed to meet the demands of advanced applications across multiple industries.
Conclusion
With unique properties, Niobium C103 alloy has become invaluable in high-temperature and aerospace applications. Its ability to withstand extreme heat, resist corrosion, and offer excellent formability positions it as a top choice in industries requiring high-performance materials. When compared to other superalloys, Niobium C103’s superior heat resistance and lightweight characteristics make it particularly advantageous for aerospace and turbine applications.
REVIEWS
{{viewsNumber}}
Thought On "{{blogTitle}}"
LEVE A REPLY(Cancle reply)
Your email address will not be published. Required fields are marked*
{{item.children[0].name}}
{{item.children[0].created_at}}
{{item.children[0].content}}
More Replies
LEAVE A REPLY
Your email address will not be published. Required fields are marked*